Case Study of Equipment Installation at a Client Company's Overseas Location (Philippines Factory)
1. Background and Purpose of Implementation
In the Philippines factory, there was a pressing need to enhance the precision of quality assurance during the shipping process. Products are packaged using materials such as silica gel and bands before they are shipped, but because these specifications vary by customer, errors were more likely to occur. In particular, once the items are wrapped in aluminum packaging, it becomes impossible to inspect the contents. Therefore, it was necessary to guarantee the packaging condition prior to aluminum wrapping and to retain evidence of it.
Since the same operations were already in place at the Ogaki factory in Japan, a decision was made to introduce the packaging form recognition device in the Philippines factory as well, in order to achieve an equivalent level of shipping assurance.
Background of Implementation | With the conventional inspection method, it was not possible to accommodate various packaging specifications, making it a challenge to improve the precision of quality assurance. |
---|---|
Purpose of Implementation |
|
Key Factors in the Decision to Implement |
|
The packaging form recognition device is designed to be integrated into existing workflows, enabling automated checks of packaging conditions without altering the workers’ established procedures.
-
Product Receipt and Preparation
-
Band
-
Automatic Detection and Automated Judgment
-
Vacuum Packaging
When the product comes out of the equipment, an operator takes it, places the designated materials, and secures them with a band. Then, upon placing the product on the rail, a mounted camera automatically detects it. AI-based object detection technology then evaluates the packaging condition as either OK or NG. If the result is OK, a “ping-pong” sound is played; if it’s NG, an alarm sound notifies the operator.
After confirming the result, the operator places the product in an aluminum bag and performs vacuum packaging. Through this system, packaging condition checks and judgments are conducted automatically, enhancing the precision of quality assurance without compromising work efficiency or productivity.
2. Post-Implementation Operation and Impact
As a result of the implementation, at a site where roughly 90% of inspections previously had errors, the number of customer complaints dropped to zero. By reliably retaining evidence, quality assurance was strengthened. Based on estimates, eliminating complaints is expected to save approximately 3 million yen per complaint.
Local staff have given high praise, stating, “There used to be times when we nearly made mistakes or actually did make them, but thanks to this device, we can now work with peace of mind” and “The workload has been reduced, and we no longer have concerns about quality control.”
Trend in Confirmation Error Rate
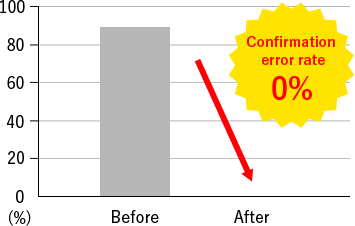
Comparison Before and After System Implementation
Before Implementation | After Implementation | |
---|---|---|
Confirmation Error Rate | Approximately 90% | 0% |
Number of Complaints | Frequent Occurrences | 0 Cases |
Cost Reduction Value | - | Approximately 3 million yen |
3. Future Outlook
The packaging form recognition device can be utilized in any factory that needs to accommodate a wide variety of packaging specifications. In particular, the Southeast Asian market is seeing a surge in demand for high-precision inspection systems, making our packaging form recognition device a powerful solution to meet those needs.
- Companies wishing to strengthen quality assurance at their overseas factories
- Production lines aiming to reduce errors and prevent complaints
- Factories seeking to retain evidence and ensure traceability
Looking ahead, we will actively expand into overseas factories—especially those in Southeast Asia—and work toward establishing a global quality assurance framework.