取引先企業の海外拠点(フィリピン工場)における装置導入事例
1.導入の背景と目的
フィリピン工場では、出荷工程における品質保証の精度向上が求められていました。
製品は出荷前にシリカゲルやバンドなどの資材を使って梱包されますが、これらの仕様はユーザーごとに異なり、ミスが発生しやすい状況でした。特に、アルミ包装後は内部の確認ができなくなるため、アルミ包装前の梱包状態を保証し、エビデンスを残す必要がありました。
国内の大垣工場ではすでに同様の業務を行っており、フィリピン工場でも同等の出荷保証レベルを実現するため、包装形態認識装置の導入が決定されました。
導入の背景 | 従来の検査方法では、多様な梱包仕様に対応できず、品質保証の精度向上が課題だった |
---|---|
導入の目的 |
|
導入の決め手 |
|
包装形態認識装置は、既存の作業フローに組み込まれるよう設計されており、作業員の手順を維持したまま、梱包状態の確認を自動化できるシステムです。
-
製品受取・準備
-
バンド
-
自動検知・自動判定
-
真空包装
製品が設備から出てきたら作業員が受け取り、指定された資材を載せ、バンドで固定します。
その後、製品をレール上に置くと、設置されたカメラが自動的に製品を検知し、AIによる物体検知技術で梱包状態のOK・NG判定を行います。判定結果は、OKであればピンポンという音で、NGであればアラーム音で作業員に通知されます。
作業員は判定結果を確認後、製品をアルミ袋に入れ、真空包装します。
このシステムにより、自動的に梱包状態のチェックと判定を行うことができ、作業性と生産性を損なうことなく品質保証の精度を高めることが可能となります。
2.システム導入後の運用と効果
導入の結果、従来は確認ミスが約9割に上っていた現場で、クレーム発生はゼロに至りました。エビデンスを確実に残すことで、品質保証が徹底され、試算ではクレームがゼロとなったことにより300万円/クレームの経費削減が見込まれています。
現地スタッフからも「今まで間違いそうになったり、実際に間違えたりすることがあったが、この装置のおかげで安心して作業できるようになった」「作業の負担が軽減され、品質管理への不安がなくなった」と高い評価をいただきました。
確認ミス率の推移
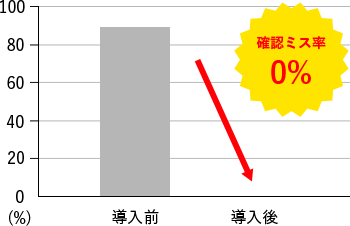
システム導入前後の比較
導入前 | 導入後 | |
---|---|---|
確認ミス率 | 約90% | 0% |
クレーム件数 | 多発 | 0件 |
経費削減値 | - | 約300万円 |
3.今後の展開
包装形態認識装置は、多種多様な梱包仕様に対応する必要がある工場であれば、どこでも活用可能します。
特に東南アジア市場においては、各国の工場が高精度な検査システムの導入を求める動きが活発化しており、弊社の包装形態認識装置はそのニーズに応える有力なソリューションとなっています。
- 海外工場の品質保証を強化したい企業
- 作業ミスを削減し、クレームを防ぎたい生産ライン
- エビデンスを残し、トレーサビリティを確保したい工場
今後も東南アジア市場を中心とした海外工場への展開を積極的に進め、グローバルな品質保証体制の確立を積極的に進めてまいります。